Visual Testing (VT) is one of the oldest and most widely used methods of Non-Destructive Testing (NDT). It’s often the first step in inspection processes, offering a straightforward way to identify surface defects and quality concerns in materials. While it may seem simple, VT is crucial for ensuring the reliability of various components across industries like manufacturing, aerospace, and power generation.
What is Visual Testing?
Visual Testing, sometimes called visual inspection, is used to evaluate materials, components, or systems for defects that are visible to the naked eye or with the aid of tools like magnifiers and borescopes. By assessing aspects like surface finish, weld quality, and alignment, VT helps detect surface-level cracks, porosity, corrosion, and other anomalies that may compromise integrity.
The Principles Behind Visual Testing
The success of VT depends on a few critical principles. First, adequate lighting is essential. Without proper illumination, even the sharpest eyes might miss subtle flaws. In addition to light, contrast plays a significant role in visibility—differences in colour, brightness, or texture between a flaw and its surrounding material make detection easier. The perception of these details also relies on the human eye’s limitations, which can be extended with tools like magnifying lenses and remote visual inspection systems.
Types of Visual Testing
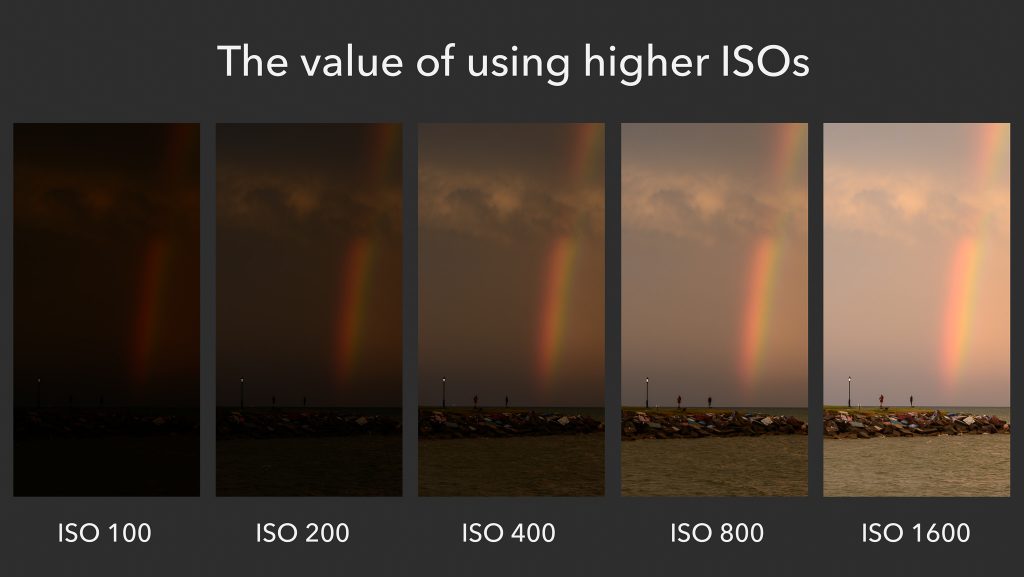
VT can be direct or indirect. Direct Visual Testing involves inspecting the object within close range using the naked eye, sometimes enhanced by tools such as mirrors or magnifiers. Indirect Visual Testing (or Remote VT) employs tools like borescopes, video scopes, and fiber optics to observe areas that are otherwise difficult to access.
Direct Visual Testing is straightforward, relying on an inspector’s eyesight and basic tools. It’s effective for accessible areas and offers real-time assessment. Indirect Visual Testing, on the other hand, uses specialized equipment to inspect inside pipes, engines, and other hard-to-reach areas. It provides clear images and can even be used in hazardous environments through remote operation.
Equipment Used in Visual Testing
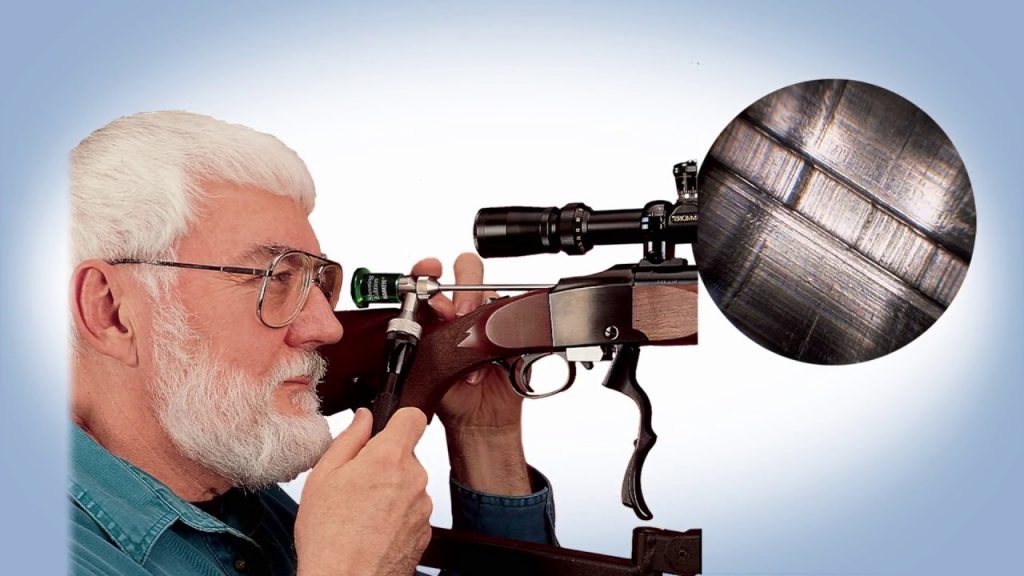
Visual Testing requires various tools, from basic mirrors and magnifiers to sophisticated borescopes and video scopes. Mirrors help in viewing behind corners or inside cavities, while magnifiers allow for a closer inspection of small or intricate areas. Borescopes and fibre-optic scopes are used for indirect inspections, providing a high level of detail and allowing for documentation via photos or videos.
Applications of Visual Testing
Visual Testing is applied throughout the life cycle of a component, from initial manufacturing to in-service inspections. In weld inspection, for example, VT identifies surface defects like cracks and undercuts, ensuring weld quality. It’s also employed in the inspection of castings, detecting issues like porosity and cold shuts that occur during the casting process. In industries like nuclear power, remote VT enables inspections in high-radiation areas where direct human involvement is not feasible.
Advantages and Limitations
VT is valued for its simplicity and cost-effectiveness. It can be performed quickly, often without the need for elaborate equipment. However, VT is limited to surface defects and requires a trained inspector with good visual acuity. Additionally, VT depends on adequate lighting, and it might not detect defects below the surface. In such cases, other NDT methods like Ultrasonic Testing or Magnetic Particle Inspection are necessary.
At Kuzer Technical, we offer comprehensive training in Visual Testing, equipping you with the skills needed for effective inspection. Reach out to us today to learn more about our courses and how VT can enhance your inspection capabilities! Contact us