Radiographic Testing (RT), a powerful and versatile Non-Destructive Testing (NDT) method that relies on ionising radiation to inspect materials for internal flaws. Imagine using X-rays or gamma rays to peer into the hidden structure of a material, revealing any weaknesses or irregularities without causing damage. This method has been instrumental in various industries, offering insights into components from electronic circuits to massive aircraft.
What is Radiographic Testing?
Radiographic Testing, or RT, is a technique that uses X-rays or gamma rays to capture images of the internal features of a material. By placing the object between a radiation source and a detector (like photographic film or digital sensors), RT produces a radiograph, similar to a medical X-ray. This method is particularly effective for detecting hidden defects, such as cracks, voids, or inclusions, making it invaluable in fields like aerospace, automotive, and construction.
How Radiographic Testing Works
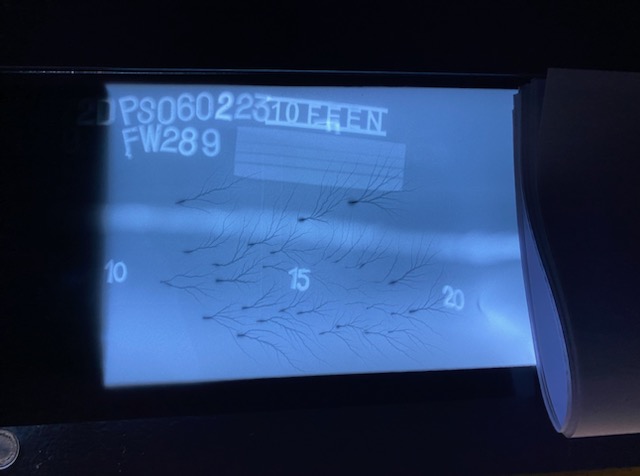
Let’s break down the process step-by-step:
- Setting up the Source and Detector: The radiation source (either an X-ray machine or a radioactive isotope) is placed on one side of the object, while a detector, usually photographic film or a digital sensor, is positioned on the opposite side.
- Radiation Penetration: The source emits ionising radiation that penetrates the material. As the radiation passes through, variations in material thickness or density affect the amount of radiation that reaches the detector.
- Image Capture: The detector captures the transmitted radiation, creating a radiograph. Areas where the material is denser or thicker appear lighter on the image, while less dense or thinner areas appear darker.
- Developing the Image: If using film, the exposed film is developed in a darkroom, revealing a permanent negative image of the object’s internal structure.
Types of Radiographic Testing
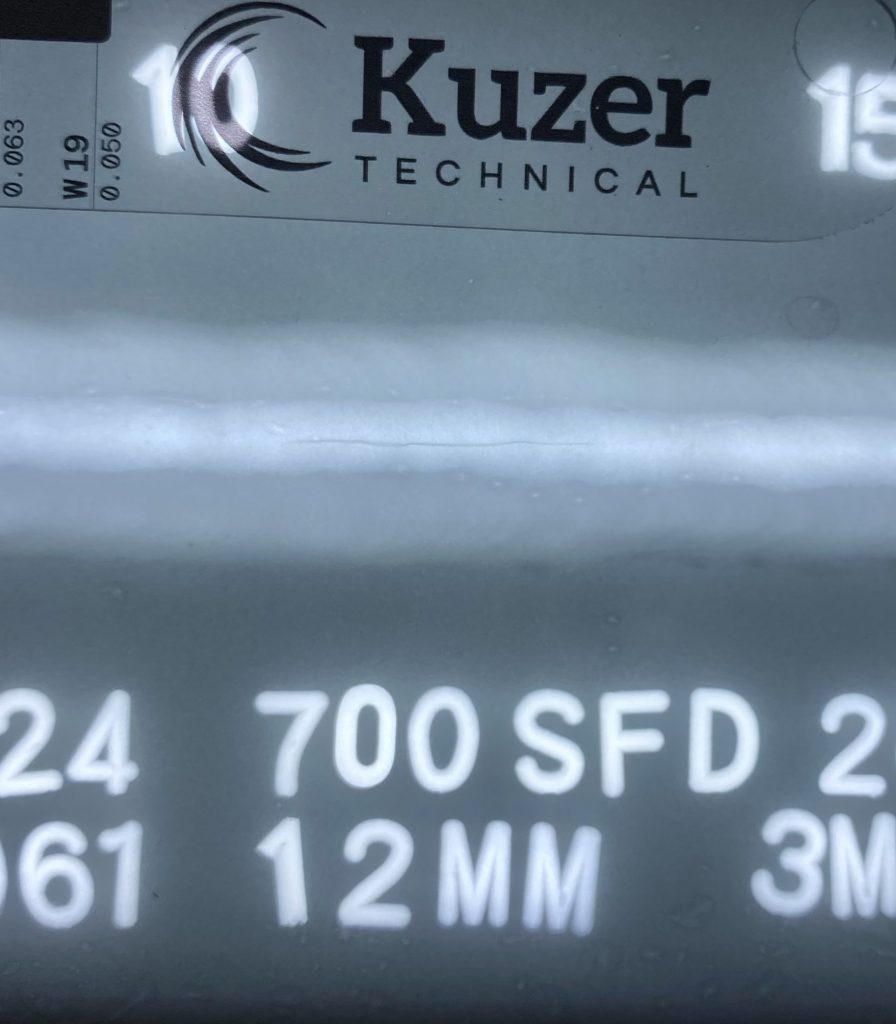
Radiographic Testing encompasses both traditional film radiography and digital methods:
- Film Radiography: The traditional method where photographic film captures the image, requiring chemical processing.
- Computed Radiography (CR): Uses reusable phosphor imaging plates that are digitally scanned to produce an image.
- Digital Radiography (DR): Captures images instantly on a digital detector, offering quick results and high resolution.
- Real-Time Radiography (RTR): Provides real-time imaging using a fluorescent screen and camera, ideal for applications needing immediate feedback.
Sources of Radiation in RT
There are two primary sources of radiation in RT:
- X-rays: Produced by an X-ray tube, offering adjustable energy levels suited for various material thicknesses.
- Gamma Rays: Emitted from radioactive isotopes like Iridium-192 or Cobalt-60, typically used for thicker materials or when portability is needed since these sources don’t require electricity.
Benefits and Limitations
RT is widely favoured for its ability to detect hidden defects and its application versatility. However, it does have limitations:
- Only Detects Density Variations: RT excels at detecting density changes but is less effective for surface defects compared to other NDT methods.
- Safety Precautions: Due to ionising radiation, RT requires strict safety measures to protect operators and nearby personnel.
Applications of Radiographic Testing
Radiographic Testing plays a critical role in various industries:
- Automotive: Inspects welds, castings, and components for flaws that could affect vehicle safety and performance.
- Aerospace: Ensures the integrity of critical components like turbine blades and aircraft structures.
- Construction: Used for inspecting welds and reinforcing materials in structural components.
RT provides a non-invasive way to assess the safety and reliability of materials, making it a staple in quality control and preventive maintenance.
Get in Touch
To learn more about Radiographic Testing and its applications!: Contact us