Welcome to the fascinating world of Non-Destructive Testing (NDT), specifically the method of Magnetic Particle Inspection (MT). Whether you’re just starting out or looking to brush up on your basics, magnetic particle testing is a crucial technique for identifying surface and near-surface flaws in ferromagnetic materials. This article will provide an overview of MPI, highlighting its core principles, the equipment involved, and some practical applications.
What is Magnetic Particle Inspection?
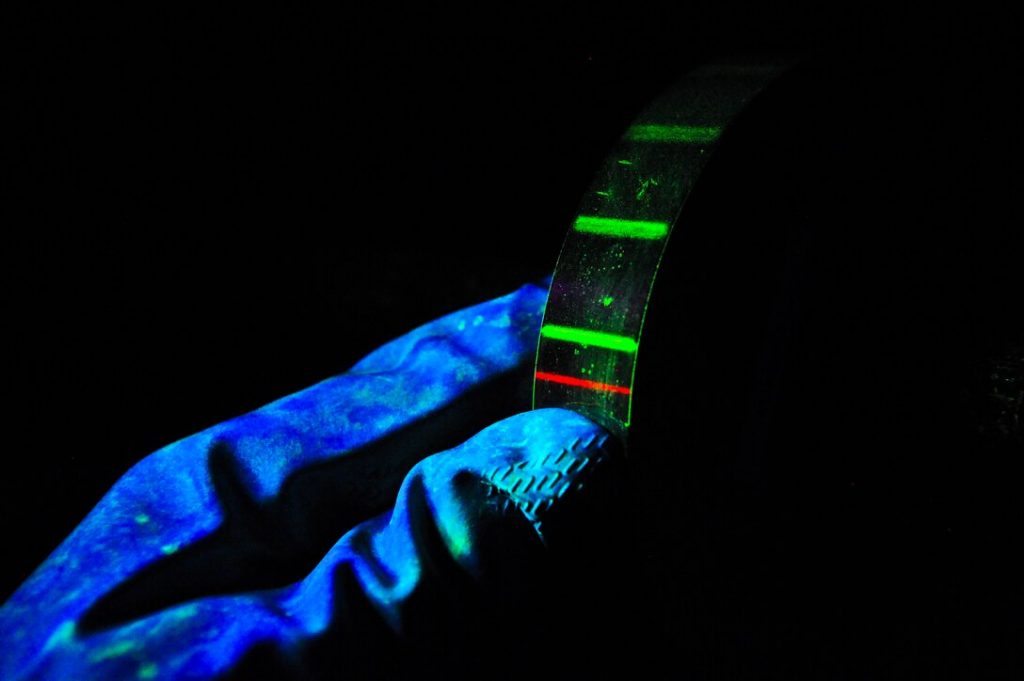
Magnetic Particle Inspection is a method used to detect flaws in ferrous materials (like iron or steel) by utilizing magnetic fields and ferromagnetic particles. It’s primarily chosen for its ability to reveal both surface and slightly subsurface defects without causing damage to the object being tested. This makes it an invaluable tool in industries where safety and integrity of materials are critical, such as aerospace, automotive, and construction.
The core principle behind MT is straightforward: when a ferromagnetic material is magnetized, and there’s a defect on or near its surface, the magnetic field will leak out at the discontinuity. By applying ferromagnetic particles to the surface, these particles are drawn to the leakage fields, visually revealing the defect.
The Basics of Magnetism in MT
Magnetism is at the heart of MT, and understanding a few magnetic properties can give you insight into why this method works so well:
- Magnetic Permeability: This tells us how easily a material can support a magnetic field. Think of it as how well a forest lets you walk through it. Materials like iron and steel have high magnetic permeability, making them ideal for MT.
- Domains: In ferromagnetic materials, atoms form regions called domains, where magnetic moments are aligned. When these materials are magnetized, these domains align along the field, creating an overall magnetic effect.
- Magnetic Fields and Flux Lines: Magnetic fields around a material are visualized as lines of flux. These lines are densest where the magnetic force is strongest. When a defect interrupts these lines, the field ‘leaks’ out, which is what MT detects.
The MT Process in Action
The MT process involves several steps to ensure thorough inspection:
- Magnetization: The part is magnetized to a sufficient point. The choice of method depends on the material and the type of defect you’re looking to find. For example, direct current (DC) is often used for subsurface defects, while alternating current (AC) is best for surface flaws.
- Applying Particles: Magnetic particles, either dry or suspended in a liquid, are applied to the material’s surface. Fluorescent particles are used under UV light for high-contrast detection, making defects more visible.
- Inspection and Interpretation: After applying the particles, you’ll look for patterns that indicate flaws. These particles attract around areas where the magnetic field leaks, forming visible indications of potential issues.
- Demagnetization: Once the inspection is complete, the part is usually demagnetized to remove any residual magnetic field, which could interfere with future use or further testing.
Equipment Essentials for MT
MT involves a range of equipment, each serving a specific purpose to enhance inspection accuracy:
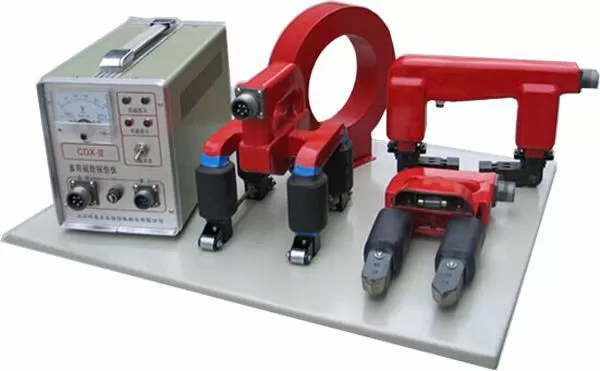
- Magnetic Yokes: These are U-shaped electromagnets placed on the material to induce a magnetic field. They can operate with AC or DC currents, depending on the inspection needs.
- Probes and Coils: Used for creating circular or longitudinal magnetization. These are typically used when parts are irregularly shaped or difficult to magnetize with a yoke.
- Field Indicators: Small, portable devices that help measure the strength and direction of magnetic fields. They ensure that the part has been magnetized adequately for effective inspection.
- UV Lights: If using fluorescent particles, UV lights are essential for making flaws more visible. The UV light causes the particles to fluoresce, highlighting any areas of leakage fields clearly.
Practical Applications and Considerations
Magnetic Particle Inspection is valued not only for its effectiveness but also for its versatility. It can be used on various shapes and sizes of ferromagnetic parts, from tiny bolts to massive steel beams. However, MT is limited to ferromagnetic materials, meaning it won’t work on non-magnetic metals like aluminium or copper.
One key advantage of MT is its ability to detect even subsurface defects, which could otherwise go unnoticed with other surface-only inspection methods like dye penetrant testing. This makes MT particularly useful for critical components where safety and reliability are paramount.
Get in contact with us today to explore more learning options and courses: Contact us