Let’s begin with a simple thought: If someone has never done any Non-Destructive Testing (NDT), this is the course they need. Imagine you’re a detective. But instead of solving crimes, you’re solving mysteries hidden within materials—unseen flaws that could be lurking, waiting to cause trouble. Welcome to the world of NDT, where we can look inside objects without breaking them apart. This is your journey through a field where the smallest crack can be a colossal clue.
Why Material Science is Crucial in NDT
At the heart of NDT lies a profound understanding of material science. Here’s why it’s indispensable: every material, from steel to ceramics, has unique properties that influence how it responds to stress, strain, and defects. Material science gives us the tools to understand these responses, enabling us to choose the right NDT methods and accurately interpret results.
When you know the molecular structure of a material, you’re not just looking at it from the outside; you’re understanding how it behaves under different conditions. This knowledge is what allows us to anticipate where flaws might form, how they’ll grow, and the risk they pose. For example, knowing that certain metals become brittle at low temperatures can guide inspectors to focus on those areas prone to cracking. Material science, therefore, transforms NDT from a basic inspection technique into a powerful diagnostic tool, essential for predicting material behavior and ensuring safety.
The Fundamentals of NDT: What You Need to Know
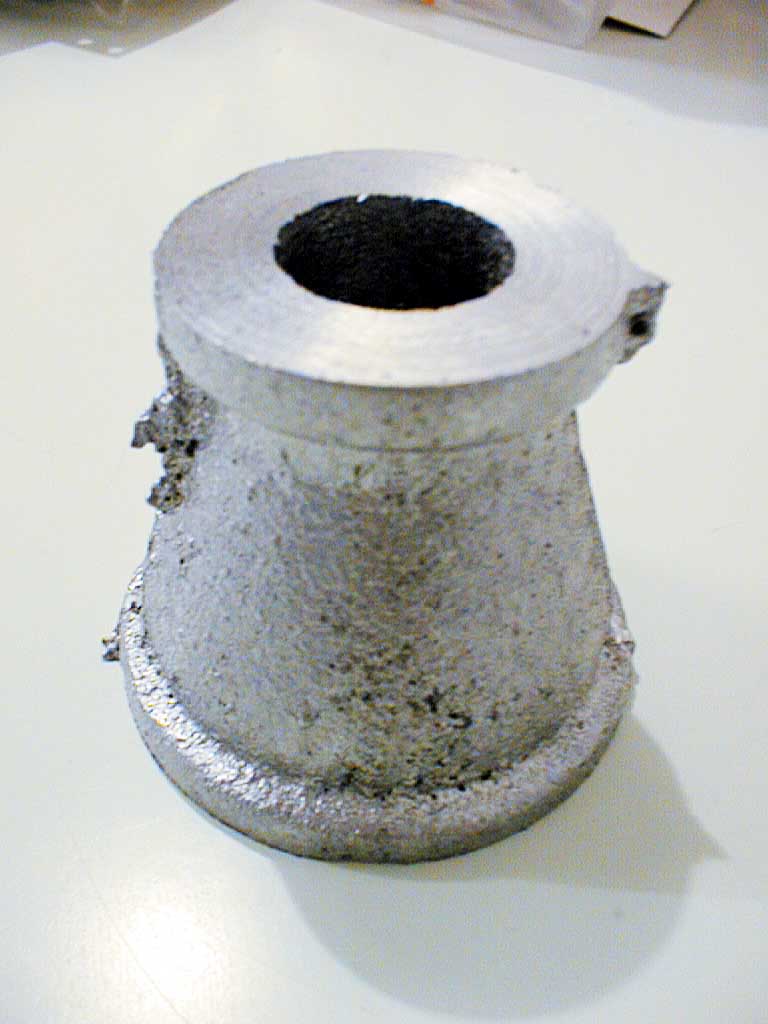
Every NDT method, no matter how advanced, is built upon a few core fundamentals that make the process possible. These fundamentals provide a roadmap for understanding and applying NDT techniques across different materials and scenarios. Here’s a quick look at what lies at the heart of NDT:
- Testing Medium Interaction: In all NDT methods, a medium—whether sound waves, magnetic fields, dye, or radiation—is applied to the material. The way this medium interacts with the material depends on its structure and composition.
- Response to Defects: When the testing medium encounters an irregularity, such as a crack or void, it responds in a way that reveals the defect’s location and nature. This change could be a reflection, absorption, or dispersion of the medium, which signals the presence of a flaw.
- Detection and Interpretation: After the medium interacts with the material, the resulting signals must be interpreted. The signals reveal information about the flaw’s size, shape, and position. Skilled NDT technicians analyze these signals to determine if a defect is present and assess its potential impact.
- Non-Intrusive Inspection: NDT is all about preserving the material’s integrity. Unlike destructive testing, where a material must be broken or altered to test it, NDT keeps the material intact, allowing for future use and re-testing if needed.
Understanding these fundamentals helps NDT technicians not only select the best method for each situation but also refine their technique to ensure reliable, accurate results. These principles are universal across all NDT methods, ensuring that whether you’re examining a steel bridge or a composite aircraft wing, you have the tools to find flaws without causing any harm.
Why We Need NDT
NDT lets us inspect materials for hidden flaws, all without damaging the item itself. It’s kind of like having X-ray vision, except you don’t need superpowers—just some nifty techniques. Picture yourself manufacturing a high-performance car engine. The last thing you want is for that engine to fail once it’s on the road. With NDT, we can catch those hidden defects before they become problems. It’s all about keeping things safe, reliable, and in tip-top shape.
The Methods of NDT: Tools for Every Mystery
There are many methods in the NDT toolkit, each suited to a different kind of mystery. Here’s a quick look at the most common ones:
- Visual Testing (VT): The simplest form of NDT—just look! With the right lighting and some specialized tools, a trained eye can catch surface flaws. This method is often the first step, kind of like getting the lay of the land before digging deeper.
- Magnetic Particle Testing (MT): Great for ferromagnetic materials, this method uses magnetic fields to expose surface and slightly subsurface flaws. Imagine sprinkling iron filings around a crack; they’d gather, making the crack visible. That’s MT for you—using magnetism to reveal hidden imperfections.
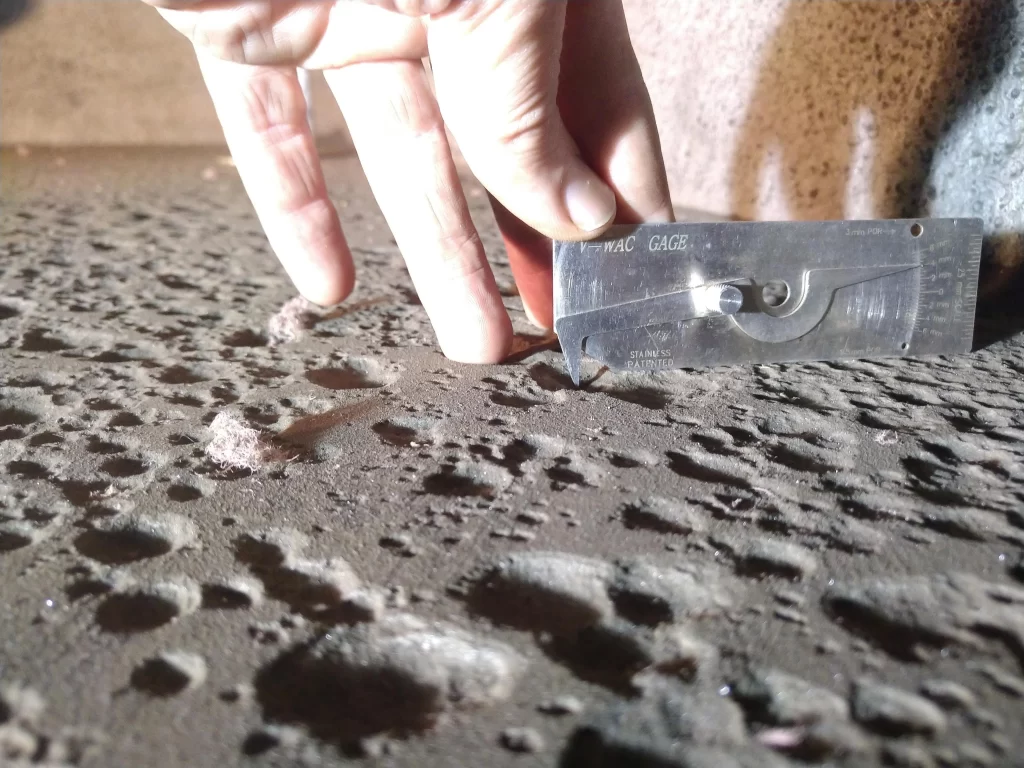
- Dye Penetrant Testing (PT): A liquid dye seeps into surface flaws, which are then revealed under UV light. This is perfect for non-porous materials and lets you see even the tiniest of cracks.
- Ultrasonic Testing (UT): Here’s where things get high-tech. UT uses sound waves to penetrate materials and reflect back information about what’s inside. Imagine yelling into a canyon and listening to the echo. UT lets us “hear” defects inside materials, even if they’re deep beneath the surface.
- Radiographic Testing (RT): Think X-rays or gamma rays. We can see inside materials just like a doctor looks inside your bones. This method is fantastic for complex structures but requires safety precautions due to the radiation involved.
- Eddy Current Testing (ET): Perfect for conductive materials, ET measures how eddy currents flow around flaws, revealing their size and location. It’s like a dance of electrons, disrupted by hidden imperfections.
Each method offers unique advantages and limitations. For instance, RT provides a permanent record, but you need access to both sides of the material. UT can probe deeply, but you need a skilled technician to interpret the results. In the end, selecting the right method is about understanding both the material and the mystery you’re trying to solve.
The Principles of NDT: See Without Touching
All NDT methods share a few principles. They use a testing medium—like magnetic fields, dye, or sound waves—that interacts with the material. This interaction changes when it encounters a flaw, and we interpret those changes to find hidden imperfections. This way, NDT is like a dance between the testing medium and the material, revealing secrets with every step.
NDT isn’t just about finding flaws; it’s also about ensuring quality and safety. By catching defects early, companies can avoid costly repairs and prevent potential disasters. Whether it’s inspecting airplane wings or bridge supports, NDT plays a crucial role in keeping our world safe.
Contact us today to learn more!