In ultrasonics, where pinpoint accuracy is essential, small miscalculations can turn your results upside down. Enter the wedge, a humble but critical component. If its wear pins extend even slightly beyond the surface, you may be in for a rude awakening as unwanted echoes and signal distortions creep into your inspection.
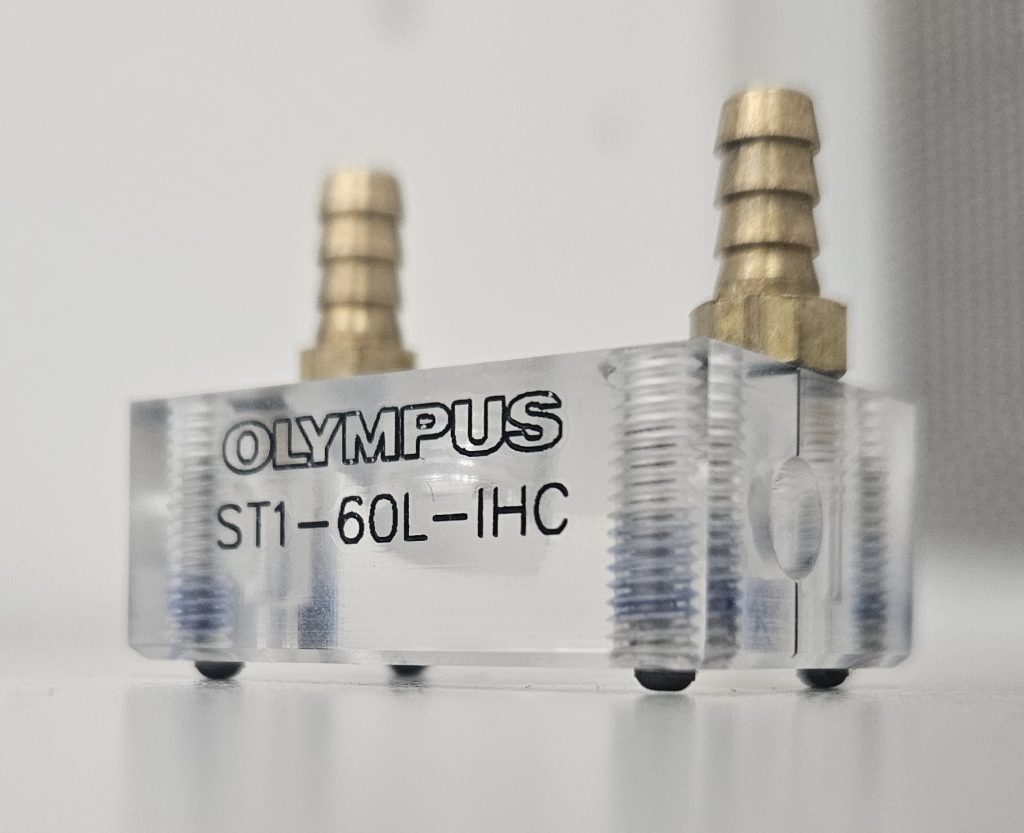
The Wear Pin Predicament
At the heart of wedge protection are wear pins – those small, usually carbide components that shield the wedge’s edges. But here’s the catch: for optimal results these pins need to be flush (or very close to) with the wedge surface. Even a slight stick out can open Pandora’s box of ultrasonic nightmares.
Imagine this: you’re conducting a critical inspection, and your wear pins are protruding just a hair’s width. That tiny gap – we’re talking as small as 50-60 microns – can introduce water pockets, create unwanted echoes, and distort your signals.
The Frequency Factor
In ultrasonic testing, the wavelength of your sound waves plays a crucial role in how these gaps affect your results.
If your gap matches a quarter of your wavelength, you might see an unexpected boost in signal amplitude and the pulse length. It’s not a good thing – longer pulse lengths directly affect resolution (and are especially critical with TOFD)
Hit the half-wavelength mark, and your signal could drop off a cliff. Suddenly, that flaw you’re looking for might as well be invisible.
TOFD Troubles: The Lateral Wave Menace
For TOFD users, gaps bring an extra headache: lateral wave multiples. Picture this: you’re looking at your A-scan, and instead of a clean lateral wave followed by potential flaw signals, you see a series of echoes. It’s like having a stutter in your ultrasonic voice. These multiples can mask critical flaws and extend your dead zone, essentially blinding you to near-surface defects.
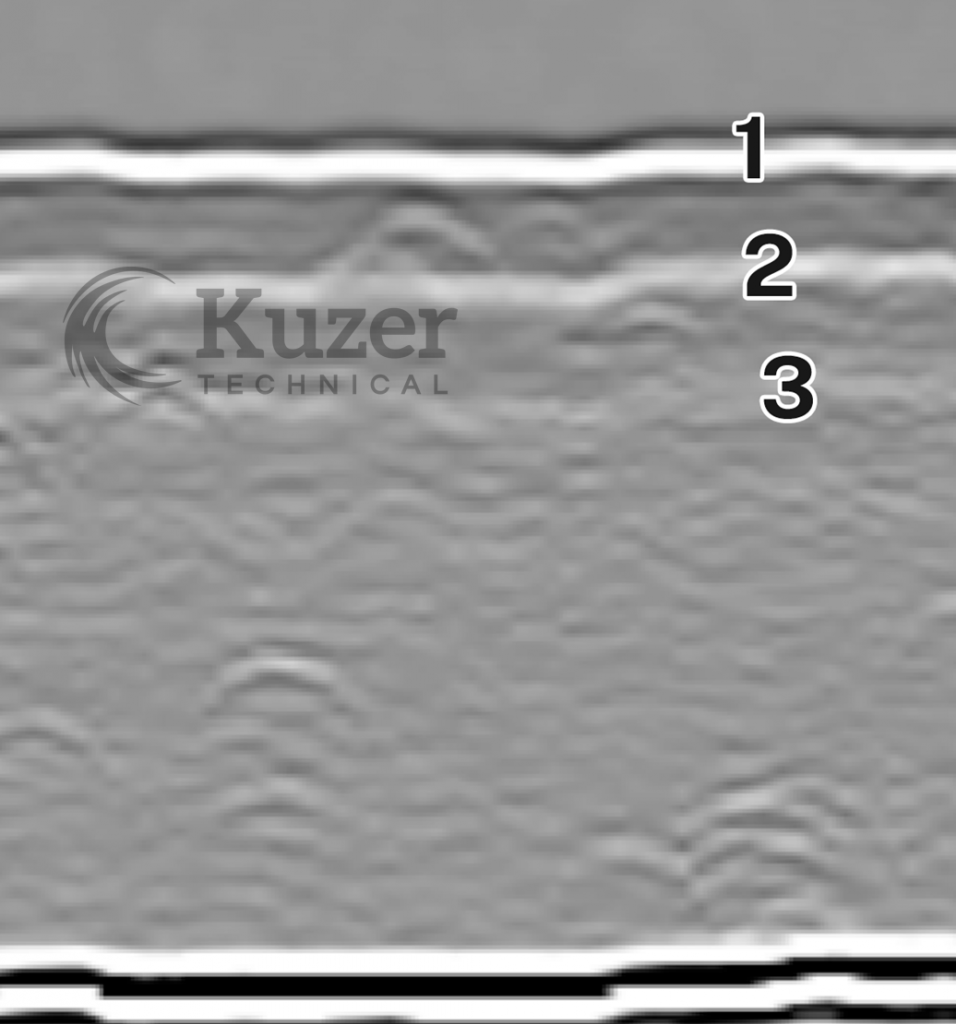
PAUT Problems: A Blurry Vision
PAUT doesn’t escape unscathed either. Those tiny gaps can wreak havoc on your carefully phased beams:
Resolution takes a hit. Your once-sharp image starts looking like it needs glasses.
Amplitude loss means weaker signals, making it harder to spot and size flaws accurately.
Keeping Your Wedge in Check
So, how do we combat this microscopic problem? Here’s your action plan:
Regular Check-ups: Treat your wear pins like dental appointments – regular checks prevent bigger problems.
Quality Control: Keep an eye on your scan quality. If something looks off, it probably is.
Frequency Awareness: Know your wavelengths and how they interact with potential gaps. Remember that we’re considering the wavelengths within the couplant and not the test item.
Swift Action: Notice a misalignment? Fix it immediately. Don’t wait for it to become a bigger issue.
Surface Prep: A smooth test surface is your first defence against gaps.
The Bottom Line
In the high-stakes world of ultrasonic NDT, the devil truly is in the details. Wedge protection isn’t just about maintaining your equipment; it’s about ensuring the integrity of every inspection you perform.
Remember: don’t let a tiny gap create a grand problem!
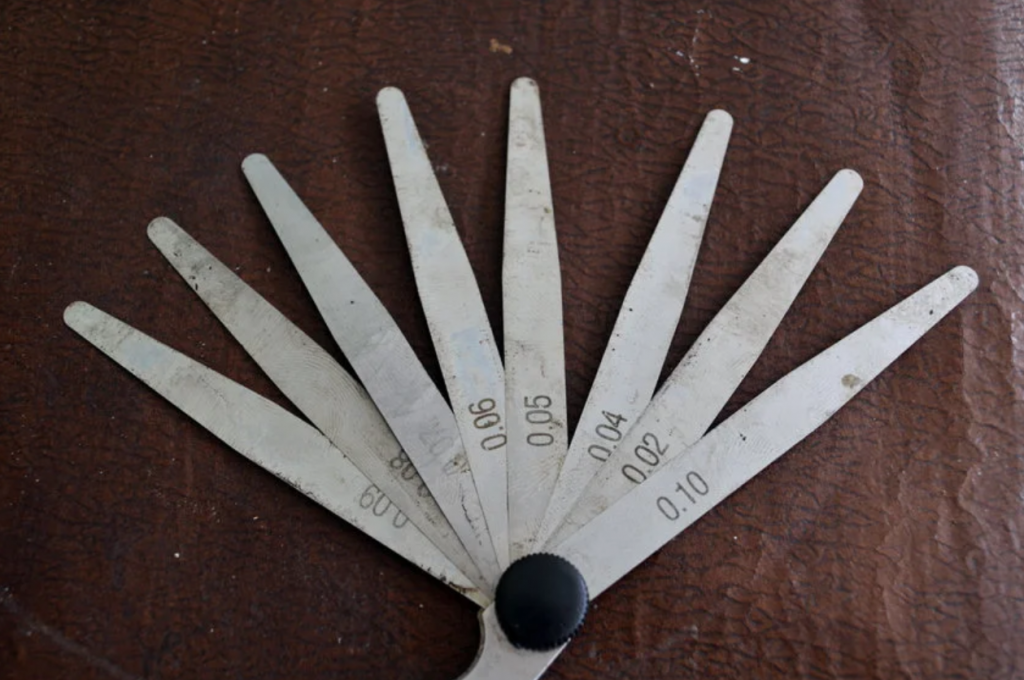